
FIM Technology
The combination of additive manufacturing (AM) and injection molding
(IM) is sometimes referred to as 3DPIM (3D-printed injection molds). 3DPIM
has substantially increased the range of materials that may be processed
through additive manufacturing, compared with stand-alone 3D-printing.
Additional benefits delivered by 3DPIM include shorter lead times and reduced
costs of product development. Recent studies show cost reductions
of 80 to 90% when metal mold inserts are replaced with 3D-printed polymer
mold inserts for short-series productions.
Now Freeform Injection Molding (FIM) – a patent-pending concept introduced
by Danish company AddiFab – adds new dimensions to 3DPIM. FIM
is based on high-precision AM and a new class of specialized printer materials,
and allows injection molding with a design freedom normally reserved
for 3D-printers. Furthermore, the entire range of injection-molded
materials is brought within the range of 3DPIM. The result is significantly
faster and more cost-efficient prototyping and short-series production.
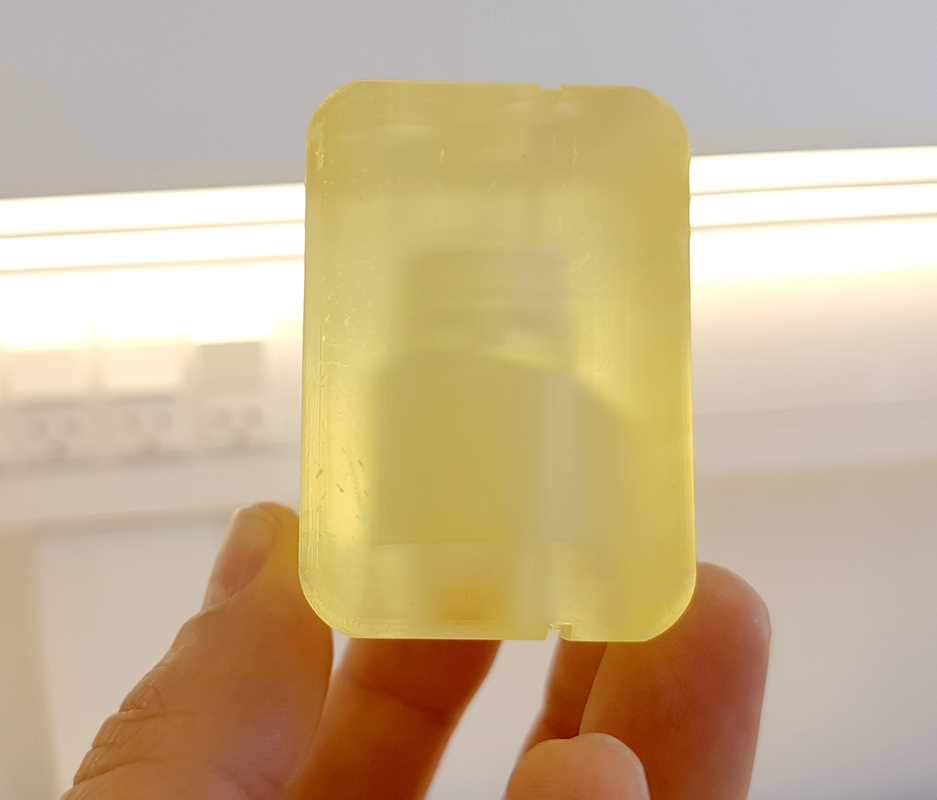

Stand-Alone AM is Challenged
for Mainstream Industrial Applications
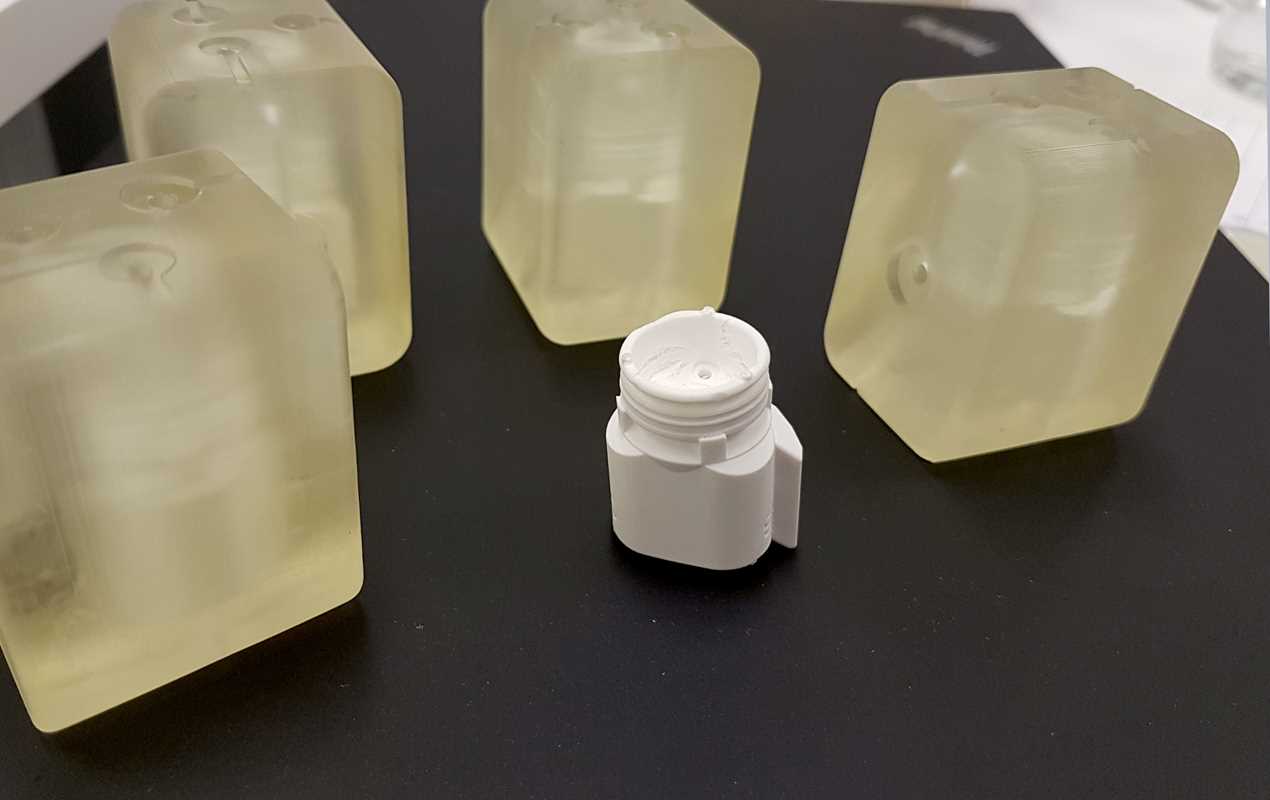
In the ideal product development model, product developers would benefit from full freedom-to-design, product launches without delays or investments, and seamless scalability.
AM has many of the characteristics that are needed to support such a product development model. These include high design flexibility, short product lead-times and low start-up costs. For those reasons, AM has become popular for prototyping and design validation. In addition, higher-end AM systems are increasingly moving into production for select high-end applications, including medical devices, automotive and avionics.
But a few important constraints reduce AM usefulness for mainstream industry:
- Limited throughput is a well-known AM constraint. While the speed of printers has increased significantly, AM still trails injection molding when it comes to the number of components that can be produced in a given period.
- Limited selection of materials is another well-known AM constraint. Even if the throughput of AM could be brought to match the throughput of injection molding, the limited selection of relevant production materials would complicate wider-spread use of AM in the industry.
- Lack of equivalence between materials processed with AM and materials processed with injection molding is a less well-described constraint. Nevertheless, the lack has far-reaching implications, especially in the medical device industry and other fields where validated material properties are critical.
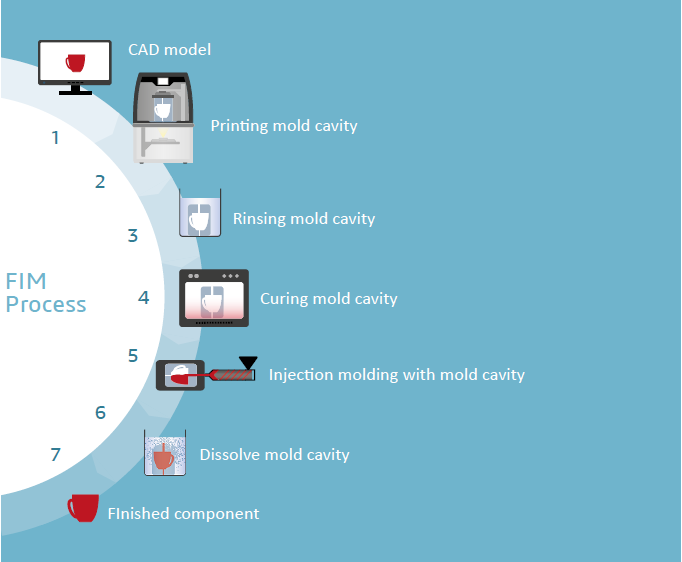
The combination of limited throughput, limited selection of relevant materials, and lack of equivalence between AM and injection molding, creates a significant barrier of adoption. Manufacturers may use AM for prototyping and product design validation, but will most often have to switch to IM for actual production due to AM constraints on throughput and available materials. However, due to the lack of equivalence between AM and IM, AM cannot be used to evaluate the performance of components that are to be injection-molded. Therefore, manufacturers moving from AM-based prototyping to IM-based volume production will have to ensure that the designs validated on AM can actually be injection-molded. And therefore, they cannot move seamlessly between AM and IM for scale-ups, short-series productions and management of variants.
Integrating AM in conventional
Injection molding process chains
In order to resolve these challenges, manufacturers have sought to integrate AM into the injection molding process chain. This integration is conceptually attractive, as it allows the low AM start-up costs and short lead-times to be combined with the scalability and wide selection of materials from IM. Accordingly, manufacturers may validate mold designs and component performance characteristics using printed injection mold cavities, and immediately move into scale-up with little or no additional validation required. Two alternative approaches exist. A first approach is based on the use of metal AM to create injection mold inserts that may comprise conformal cooling and other complex features. Such inserts are highly useful for high-volume injection molding due to superior cooling. However, high costs and limited access to required machinery and competences are limiting the relevance of this approach for prototyping and scale-up applications, especially for smaller companies.
An alternative approach, that is more readily applicable for prototyping and scale-up applications, is based on the use of lower-cost 3D-printed polymer injection mold inserts. These may be manufactured by various AM methods, and may be used for prototyping and short-series production in several standard thermoplastic materials. Research shows that the use of such polymer inserts may allow a manufacturer to reduce tooling costs for the manufacturing of 100 prototypes with 80 – 90% by switching from metal to polymer inserts for the first batch.
While the use of polymer inserts provides the product developer with an efficient tool for prototyping and short-series production, a few important limitations remain.
- The Limited selection of materials remains an issue even if the range of processable materials is substantially increased. Printed polymer inserts have been used to process a number of standard thermoplastic materials, but the method is challenged as temperatures and pressures increase. In addition, materials filled with glass-fibers or similar abrasives will quickly wear out a polymer insert. Finally, injection molding of rubbers (LSR injection molding and similar) requires mold tools with very high precision due to the low viscosities encountered. The required precision levels are near-to-impossible to achieve using 3D-printed mold inserts.
- The use of AM polymer inserts may increase the limits on geometrical freedom imposed by injection molding. In a conventional injection mold, drafts, split lines and polished surfaces are important to ensure a smooth release of the injection-molded component. While drafts and split lines may to some extent be reproduced in a polymer insert manufactured by AM, the surface roughness is significantly higher in an AM insert than in a corresponding metal insert.
This increased roughness may result in increased adhesion of the molded part to the polymer insert and may impose significant mechanical stress on each component. Components made from brittle materials cannot withstand this stress and may break apart. Ductile materials withstand the stress better but may experience warpage or distortion.
As a result of these unresolved challenges, even the integration of AM into the injection molding process chain does not provide solutions to all the problems faced by manufacturers seeking a flexible, cost-efficient and highly scalable production platform.
Freeform Injection Molding:
Merging benefits to overcome barriers
In an attempt to resolve these remaining challenges, Danish company AddiFab has introduced
Freeform Injection Molding (FIM)
Freeform Injection Molding is based on AddiFab’s Add-Line platform, which comprises a line of high-end printers and post-processing accessories. The Add-Line printers are state-of-theart DLP machines that are built to meet the exacting tolerance and repeatability requirements found in the injection molding industry. They are designed to support integration and automation, and AddiFab is continuously adding accessories that will support the precision manufacturing of AM components.
In Freeform Injection Molding, high-precision single-use one-piece mold cavities are printed using AddiFab Add-Line printers and post-processing accessories. These cavities are printed in STIM resins, a new, patent-pending class of dissolvable polymer materials developed by AddiFab. The STIM materials are at the same time very strong, very thermally stable and entirely dissolvable. The use of high-precision single-use dissolvable cavities allows
AddiFab to remove the two constraints unaddressed by conventional polymer inserts:
- FIM removes material constraints. While FIM polymer inserts are still less durable than conventional metal inserts, they have already been used to process high-temperature materials up to, and including, PEEK. Several glass-filled polymers, including PA and PPS, have also been molded with success, along with 2K rubbers, LSR rubbers and even foams. Below are shown some of the materials and geometries that have been processed to date.
- The geometrical constraints of injection molding are eliminated in FIM. Single-use dissolvable mold cavities do not require split lines or drafts and impose no physical stress on the molded components during dissolving. Several of the geometries shown above are impossible to mold using conventional injection molding, but trivial to manufacture using FIM. An additional advantage associated with dissolvable molds is that even the most fragile materials (foams, soft silicones, feedstocks for powder injection molding) may be molded using FIM. Accordingly, FIM may efficiently reduce or entirely eliminate the constraintspresently holding back the full integration of AM into the IM process chain.
Reduced Costs and Risks
in New Product Development
Our early experience with Freeform Injection Molding has led us to believe that FIM may evolve into a transformative paradigm. Research into 3DPIM has already demonstrated the massive time and cost savings that may result from using AM polymer inserts for injection mold prototyping and design validation.
With FIM, those same time and cost savings are complemented by access to a much wider range of materials and a much higher degree of design freedom. The slightly higher costs per part produced are offset by dramatic reductions in pre-market tool investments, times-to-first product and dramatic increases in responsiveness.
In addition, lower pre-market investments and times-to-first-product, combined with higher responsiveness, lead to reduced decision costs and reduced costs of failures.
The decision to invest in tooling is one of the most expensive and time-consuming decisions in the conventional product development process, and requires that a product design be frozen.2 Significant investments, combined with loss of freedom, usually require extensive and time-consuming analyses of market potential, design validity and other factors that may influence the product business case. In spite of these efforts, research has shown that an average of 40% of products fail3, which adds to the costs of bad decision making.
If pre-market investments in tooling can be reduced by a factor of 10, and design flaws can be rapidly and easily corrected through a design file update, the need for extensive pre-freeze analyses is reduced. In addition, a more iterative and responsive approach to product development and implementation of user requirements, may be pursued.
Direct printing
We offer DLP based direct printouts in 50 microns resolution on a 96 x 54 x 150mm work area. For quotation please contact via mail.
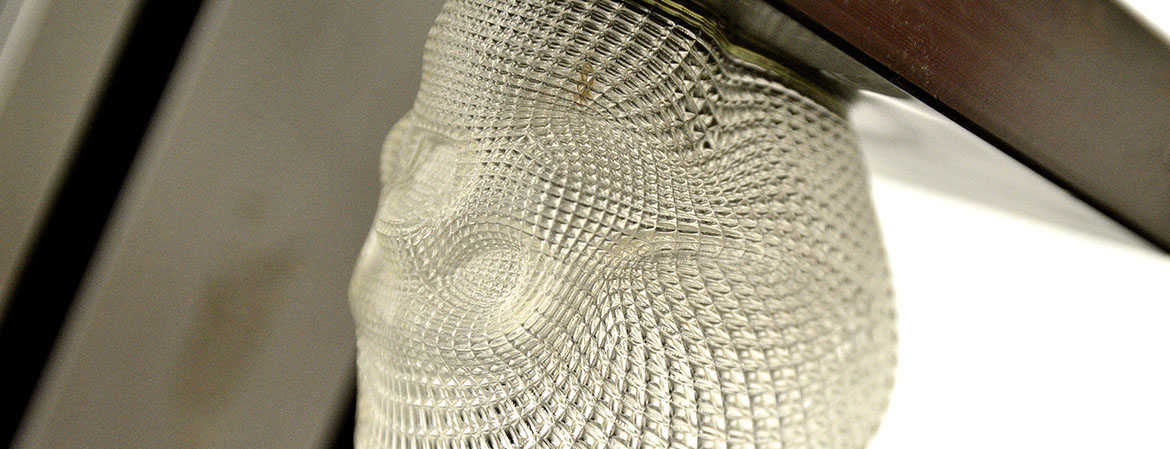
Source www.addifab.com